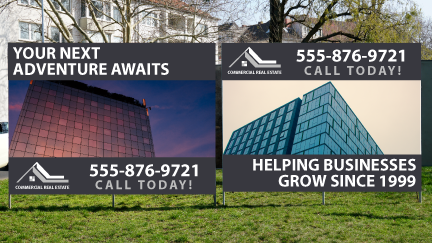
If you’re looking, you’ll see them everywhere. Often called site signs, they are generally large, rectangular signs placed in front of commercial or industrial properties for sale. You’ll see them in front of available buildings, on plots of open land, or even during the construction process.
What’s the difference between commercial and residential signage?
The primary difference between commercial and residential signage is the size. While residential signage tends to be 32×24 inch and smaller, commercial signage is often 48×36 inch and larger.
It’s not uncommon for a commercial or industrial property to have a 4×8 foot sign, or even larger, standing proud out front.
Who buys the most commercial/industrial property signage?
Most often, a commercial real estate agent or broker will foot the bill for the signage when they are contracted to represent the property. Agents will often reuse their signage once a property sells, but that doesn’t mean the sign service stops. Many sign companies sell sign removal, sign storage, and sign placement services for busy real estate agents and brokers.
Oftentimes, larger commercial properties will have multiple site signs for many of the stakeholders. The financing institution, general contractor, or even some of the subcontractors may want to place their signs on the property as well. This helps with advertising and name recognition. Few things drum up new business as well as being attached to other successful projects in your area.
How are commercial site signs made?
Large real estate signs can be as simple or as elaborate as your customer’s budget allows for. I’ll offer a few ideas here starting with the simplest and least expensive.
Frames
- Pressure treated lumber from the home center
- Painted lumber from the home center
- PVC Fence material from a local fence supplier
- Sign Frame
- SignTrac
- 4Ever Products
Sign Material (Substrates)
- 4mm Corrugated Plastic
- 6mm Corrugated Plastic
- 10mm Corrugated Plastic
- 6mm PVC
- Painted Plywood
- 3mm Aluminum Composite Material (ACM)
- 6mm Aluminum Composite Material (ACM)
- Alumicorr or Alumalite
- MDO Sign Panel
Graphics
- Plotter/cut vinyl decals applied to a blank substrate
- Digital printed vinyl, applied to a substrate
- Direct printed substrates
Placement
- Stakes pounded into soil
- Holes dug/augered
- Filled with compacted soil
- Filled with dry concrete mix and compacted soil
- Fill with mixed concrete
- Frame weighted with sandbags (For use when holes cannot be dug)
The design of the frame, choice of materials, and installation techniques are dependent on the size of the sign and availability of materials in your area. Since commercial signage can get to be very large, transportation costs can quickly erode any margin you might have.
How do I get started?
There’s a style for every skill set and budget. Understanding what to offer your clients is a challenging decision, but the only way to work that out is to get started!
First, start by driving around your area and familiarize yourself with what’s most common. Chances are good that your customers will want a sign similar to the ones they see most often. Get out and take a closeup look at the design, materials used, and mounting techniques.
In most cases, a prebuilt kit from one of the vendors listed above will be your best bet for the frame, but building a sign mounting system using lumber and materials from your local homecenter is also quite common.
Once you determine the frame you would like to use, decide on your substrate. Perhaps the most common substrate used today is a composite material made up of a plastic core with an aluminum face. There are a tremendous number of choices when it comes to aluminum composite materials. Your best bet is to start with your local wholesale sign supply and find out what they offer.
Graphics can be directly printed to the substrate, printed on an adhesive vinyl and applied to the substrate, or cut out of colored vinyl and applied in a process often referred to as cut vinyl application.
Whether you are just getting started, or a seasoned sign professional, commercial and industrial real estate signs are a great way to get started in the sign industry. There’s really no wrong way to get them done. Whether you are an experienced DIYer, or want to resell a prebuilt kit, there’s an option for every skillset and budget.